The Cost of Low Confidence: Why the Lack of Inbound Freight Visibility is the Achilles’ Heel of Effective Inventory Management
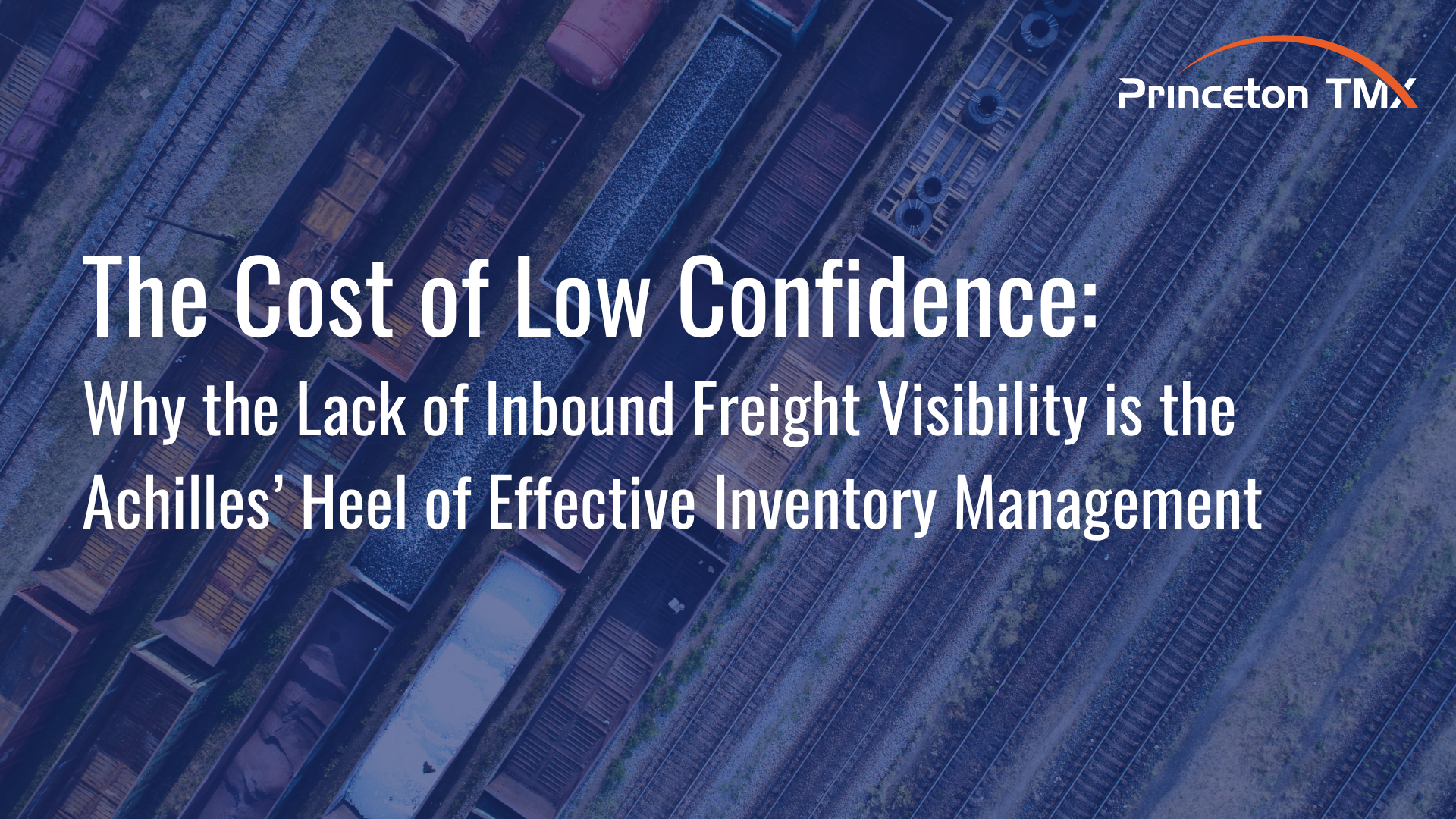
Confidence in your inventory levels is no longer a luxury, it’s a requirement for competitive logistics operations. Yet for many industrial manufacturers, that confidence is built on shaky ground. Beneath the surface of seemingly reliable systems and processes lies a hidden vulnerability: a persistent lack of visibility into inbound shipments of raw materials. While companies invest heavily in ERP systems, demand planning software, and warehouse automation, they often overlook one critical truth; you can’t manage what you can’t see. And when you lack real-time insight into when and what is arriving at your facility, every downstream decision is compromised.
Inbound Freight Blind Spots: A Strategic Risk Hiding in Plain Sight
Accurate inventory data is foundational to lean operations, production planning, and working capital efficiency. However, that inventory accuracy is on the timely and reliable flow of information upstream, particularly from transportation.
This is where the blind spot occurs.
Inbound freight, especially rail shipments of raw materials, is often the least visible part of the supply chain. Unlike truckload freight, which frequently benefits from advanced tracking systems and real-time ETA updates, rail freight can remain opaque until it physically arrives at the gate. Many railroads do not proactively provide advanced notification of shipments. Instead, manufacturers rely on lagging indicators like PO acknowledgments, bill of lading timestamps, or anecdotal updates from logistics coordinators, none of which give a comprehensive or timely picture of what is inbound and when it will arrive.
This lack of upstream visibility creates a chain reaction of inefficiency. Production planners are left to make critical decisions without full knowledge of raw material availability. Procurement teams are forced to overbuy to hedge against potential delays. Receiving teams are reactive, rather than prepared. And the finance team is left holding the bag, dealing with excess inventory and bloated carrying costs that destroy margins.
The Downstream Consequences: Planning in the Dark
The operational and financial consequences of inbound freight uncertainty are staggering and well-documented. According to McKinsey, companies with low end-to-end supply chain visibility experience inventory inaccuracy rates of up to 20%, leading to a 10–15% hit on service levels and a 15–30% increase in working capital requirements. For manufacturers dependent on a steady flow of raw materials, even a single delayed shipment can have cascading impacts: missed production targets, costly line stoppages, last-minute premium freight to recover lost time, and ultimately, delayed or canceled customer orders.
Worse, these issues compound over time. A plant forced to idle for lack of materials doesn’t just lose productivity that day, it throws off the entire production calendar, strains labor scheduling, and reduces utilization of assets. When customers are affected, trust begins to erode, and service penalties or lost contracts can follow. In sectors like metals, mining, paper & packaging, and other industrial manufacturing verticals where downstream partners rely on just-in-time supply, the cost of uncertainty can skyrocket into the millions in just a matter of days.
And yet, many organizations continue to operate with these risks embedded in their standard processes, treating inbound visibility as a nice-to-have rather than a critical control point.
Why Rail is the Epicenter of the Problem
Rail is perhaps the most costly gap in inbound visibility for manufacturers. While it remains an efficient and cost-effective mode for moving bulk raw materials over long distances, it lags significantly in terms of real-time data transparency. Unlike truckload shipments, which can be monitored with GPS tracking, ELD integrations, or telematics platforms, rail lacks consistent standards for shipment updates and estimated arrival notifications. In some cases, shippers don’t learn that a shipment is en route until it is already on-site or missed entirely.
This gap is particularly damaging for large-volume industrial manufacturers who depend on rail for high-density materials like steel coils, plastic resin, grain, chemicals, or aggregates. These are not materials that can be easily sourced overnight or trucked in at the last minute. When rail deliveries go unmonitored or undetected until arrival, it’s not just a visibility problem, it’s a planning disaster.
The irony is that many of these same companies have invested millions into sophisticated inventory optimization tools, but the absence of reliable inbound data renders those tools ineffective. Predictive analytics is only as accurate as its inputs, and when raw materials can vanish into a black hole of uncertainty between supplier and plant, the value of the entire planning function is diminished.
Inbound Rail Freight: Breaking the Black Box with Advanced Shipment Notifications
For supply chain executives, this is a call to action. You cannot allow inbound freight to remain the blind spot of your supply chain. If you’re serious about improving inventory turns, reducing working capital, and delivering on customer commitments, you must treat inbound visibility as a strategic capability, not a tactical function delegated to the transportation team.
This requires a shift in mindset. It means moving from reactive tracking to proactive shipment notification. From tribal knowledge and email updates to structured data and systems integration. From viewing rail as a static, slow-moving piece of the puzzle to recognizing it as a vital, dynamic component that can and should deliver real-time information.
It also means asking hard questions:
- Do we know what raw materials are en route to our plants and when they’ll arrive?
- Are we able to plan production with confidence based on inbound inventory data?
- Can our systems and people adapt quickly when disruptions occur upstream?
- What is the cost to our business of not knowing?
Until these questions are answered with data, not guesswork, manufacturers will continue to suffer from preventable inefficiencies that erode margins and threaten competitiveness.
The solution to the rail freight visibility problem lies in the adoption of Advanced Shipment Notifications (ASNs), a digital mechanism for providing proactive, structured updates about shipments in transit before they arrive. Unlike traditional shipping documents that are often static, post-fact, and siloed, ASNs are designed to deliver timely and detailed information upstream in the supply chain.
For rail, this means shippers receive an early, standardized notification the moment a supplier or rail partner initiates a shipment, including what materials are on the way, when they are expected to arrive, and how those materials are configured (e.g., car type, quantity, weight, or packaging). The strategic value of this visibility is immense. ASNs empower manufacturers to align inbound material flow with production schedules, optimize dock scheduling, improve labor planning, and reduce safety stock. Most importantly, they replace guesswork with precision. In a transportation mode long plagued by lagging updates and fragmented data, ASNs represent a shift toward synchronized, anticipatory logistics.
When implemented effectively, they transform rail from a reactive bottleneck into a predictable, data-driven input that supports stronger decision-making across procurement, planning, and operations.
Conclusion: Visibility Isn’t Optional
In an era of geopolitical shocks, labor volatility, and shifting demand, the margin for supply chain error is shrinking by the day. Inventory confidence, and by extension, operational excellence, starts with knowing what’s coming before it arrives. That means elevating inbound freight visibility from a backend process to a boardroom priority.
Manufacturers who continue to tolerate freight blindness are not just operating in the dark, they’re inviting disruption. Those who build visibility into their inbound networks will not only survive the next supply chain crisis, they’ll lead through it.
The question is: Which side of that line do you want to be on?